‘Roboat’ docking system
Design of the latching and docking system for the full-scale Roboat - a prototype fleet of autonomous boats for Amsterdam’s canals (MIT / Amsterdam, 2020-21).
The mechanism makes use of a sliding-crank linkage to maximise the tolerance between the boat and its target, while working within the tight constraints provided by the boat hatches to allow the mechanisms to be fully retracted when not in use (opening up the potential for the arms of another boat to latch into the mechanism). Once deployed, spring-loaded ‘power-off’ brakes secure the final position without consuming further power.


--
Two latching mechanisms installed in the central bays of the full-scale Roboats at the Marineterrein in Amsterdam. The latching system relies on two symmetrically opposed mechanisms: a sliding-pin linkage allows each arm to make a steep exit out of the hatch before securely grabbing its target.
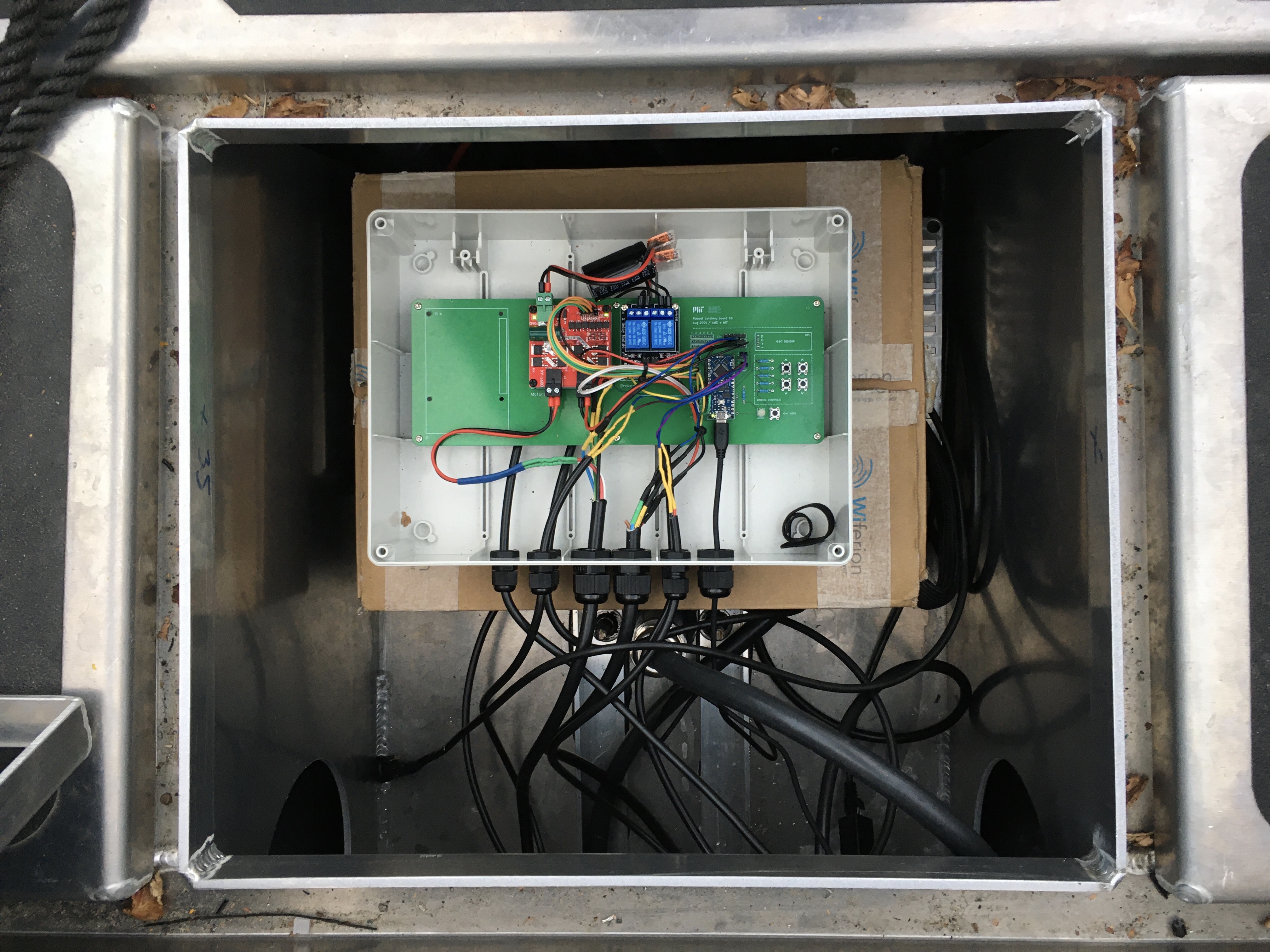
--
Iterations: early 3D-prined prototype during lockdown; milling bearing surfaces in the MIT Architecture Shops; control electronics in the full-scale prototype in Amsterdam.
--
[videos] Tests at the MIT sailing pavilion and on the full-scale passenger Roboat “Lucy” in Amsterdam.
Starting from scale 3D printed prototypes tested at home during lockdown, it was great to see this project all the way through to the installation in two full-scale boats in Amsterdam in October 2021.
--
ICRA 2022 paper.
Supervised by Daniela Rus (CSAIL) and Carlo Ratti, with David Fernandez Guttierez (software), 2021. Thanks to the rest of the MIT/AMS Roboat team, and to Shah, Chris, Jen and Zain at the MIT Architecture Shops.